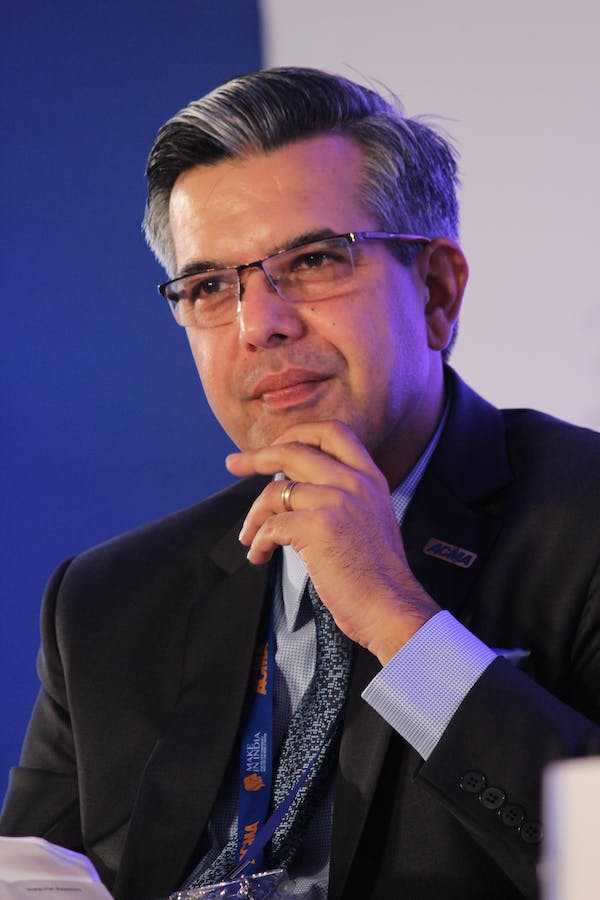
14 Jan ENGINEERING THE FUTURE: TOP 2025 MANUFACTURING TRENDS TO BE TRACKING TODAY
Manufacturing drives productivity, prosperity and economic prowess for nations worldwide. But industry dynamics face pivotal technology-driven transformations, heightened sustainability demands and competitive realignments over the next few years. Myriad trends will redefine leading manufacturers come 2025.
Industry 4.0 Scales Across Factories
Also known as smart manufacturing and the digital factory, initial Industry 4.0 pilots demonstrated the data-driven future synchronizing systems, supply chains and production lines for efficiency gains. As 5G, AI and interconnected control software mature, majority penetration scaling smart manufacturing broadly across company factories and the supply ecosystem will hit key milestones.
Additive Manufacturing Ubiquity
While 3D printing usage expanded recently, applications concentrate on prototyping and small novelty runs today. Equipment, materials and control software improvements will drive adoption suited for complex mid-volume production components across aerospace, autos and select consumer goods marking a pivotal acceleration toward additive ubiquitous manufacturing.
Mainstreaming of Exoskeletons
Ageing workforces pressured by productivity goals increase injury risks and turnover. Lightweight exoskeleton options emerging help offset fatigue and support movement for entry-level roles. Early fleet trials show huge potential. Cost effective scaling will drive utilization across 30%+ of applicable blue collar production jobs improving quality, safety and motivation.
Advanced Robotics Redefine Processes
Easy tasks automated years ago leave room for improvement across delicate complex assignments from bin picking to material finishing requiring contextual judgement like humans. Specialized cobot and AI solutions master new thresholds for flexibility handling novel classification, reactive troubleshooting and structured coordination allowing robots to permeate white collar factory domains.
Rise of Digital Twins
Modeling every component and system relationship through constantly updated virtual replicas enables what-if simulations to optimize manufacturing system outputs spanning machines, inventory and schedules based on site specific constraints. Though current twin adoption remains below 10%, scaling enablers will drive majority penetration come 2025 as larger plants experience value with each incremental integration.
Mainstream Adoption of Autonomous Mobile Robots
Automating internal logistics proves a straightforward initial automation opportunity with quick ROI. Mobile robots navigating factories autonomously reached new sophistication and value milestones recently. Cost reductions will encourage mass adoption of various form factors across manufacturing, warehousing and hospital campuses managing the majority of routinized material transport.
Brand Focus on Sustainability Grows
Demand increased for transparency within product lifecycles as ESG concerns mount. Manufacturers will overhaul packaging, emissions, raw material tracing to validatable renewable sourcing and full circularity through sophisticated blockchain enabled supply chain integrations rather than generic high level commitments showing substantive ESG action today.
Supply Chain Resilience Initiatives Accelerate
Globalization and wage arbitrage left Western supply infrastructure fragile to disasters as evidenced throughchip shortages. Using localization, friend-shoring and inventory buffers, manufacturers will rebuild flexible buffers in 2025 to sustain operations through crisis scenarios that will inevitably strike globally interconnected economies again.