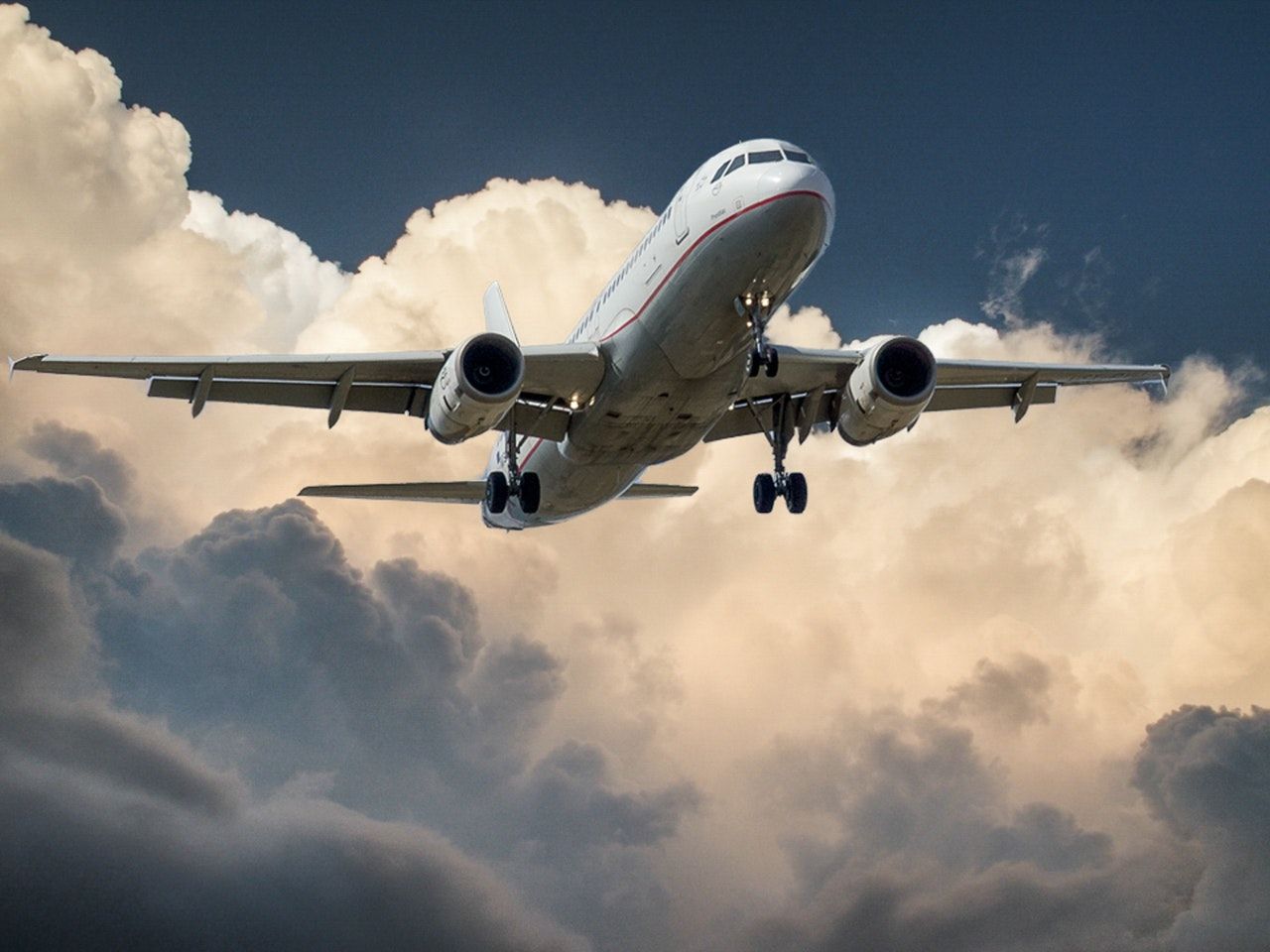
22 Jun FUTURE TRENDS IN AIRCRAFT MANUFACTURING AND ENGINES
News flash – in case you missed the memo, the aviation industry is at a turning point. Faced with growing concerns over climate change, dwindling fossil fuel resources, and increasing demands for more efficient travel, aircraft manufacturers are pursuing innovations in design, materials, and propulsion systems. The future of aircraft manufacturing and engines will therefore marked by a focus on sustainability, advanced technologies, and the integration of artificial intelligence. Ready to discuss what it might hold? Away we go then!
Right from the get-go, it’s important to consider a rising shift towards electric and hybrid propulsion systems. As the need for more sustainable and efficient air travel grows, manufacturers are investing in electric propulsion technologies that reduce greenhouse gas emissions and decrease fuel consumption. Electric aircraft, powered solely by batteries, have the potential to revolutionize short-haul flights and general aviation. Although currently limited by battery technology, advances in energy storage and power density are expected to drive the development of larger, more capable electric aircraft.
Hybrid-electric propulsion systems, which combine traditional combustion engines with electric motors, offer a more immediate solution for longer-range flights. By using electric power for takeoff and landing and combustion engines for cruising, hybrid aircraft can significantly reduce fuel consumption and emissions. Several major manufacturers, such as Airbus and Boeing, are actively working on hybrid-electric concepts that could reshape the future of commercial aviation.
That said, aircraft manufacturers are increasingly adopting advanced materials and manufacturing techniques to improve efficiency and reduce environmental impact as well. One notable development is the use of lightweight composite materials, such as carbon fiber-reinforced polymers, to replace heavier metal components. These materials not only decrease the overall weight of the aircraft but also offer increased strength and durability.
Additive manufacturing, also known as 3D printing, is another potentially game-changing technology in the future of aircraft manufacturing. This process allows manufacturers to produce complex, lightweight structures that would be difficult or impossible to create using traditional manufacturing methods. By reducing the weight and increasing the strength of aircraft components, additive manufacturing can contribute to significant fuel savings and reduced emissions.
No secret here either: Artificial intelligence (AI) is playing an increasingly important role in helping remake the future of aircraft manufacturing and engine design. Automation and AI technology can be utilized in various aspects of the industry from streamlining design processes to optimizing engine performance and predictive maintenance. Case in point: In the design phase, AI can help engineers create more efficient and aerodynamic aircraft designs by analyzing vast amounts of data and running simulations to optimize performance. This can lead to significant improvements in fuel efficiency and overall aircraft performance. On another front, AI can also be used to monitor engine performance in real-time, allowing for the early detection of potential issues and more efficient maintenance schedules. Leveraging smart tools can not only improve aircraft safety but also reduce downtime and maintenance costs.