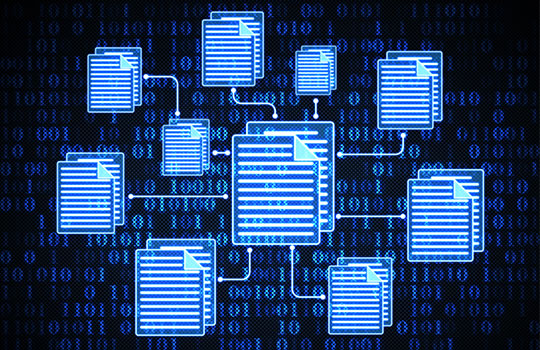
13 Apr COMPUTER CHIPS: MANUFACTURING, DISTRIBUTION AND FUTURE TRENDS
Computer chip manufacturing has been a key driver of technological advancement, enabling everything from smartphones to artificial intelligence. As technology continues to evolve, coming years are poised to bring even more breakthroughs and innovations. Here are some of the trends that we’d bet our bottom (virtual) dollar will increasingly come to define the future of computer chip manufacturing.
Right off the bat, the industry has historically relied on lithography, a process of printing patterns onto a substrate using light. Nonetheless, as chip components have become smaller and more complex, lithography has become increasingly challenging.
To overcome this challenge, new manufacturing techniques such as extreme ultraviolet (EUV) lithography and multi-patterning are being developed. These techniques enable the creation of smaller, more complex chips that can support more advanced technology.
The materials used in computer chip manufacturing are also evolving too. For example, graphene is a two-dimensional material that is extremely strong, lightweight, and conductive. Needless to say (but we’ll say it anyway), graphene has the potential to replace traditional silicon in chip manufacturing, enabling faster and more efficient processors.
Beyond this though, other new materials such as gallium nitride and silicon carbide are also being explored for use in chip manufacturing. These materials offer improved power efficiency, higher switching speeds, and better temperature tolerance.
The packaging of computer chips has traditionally been a passive process, with the chip being attached to a circuit board and covered with a protective layer too. But you should know that as chips become smaller and more complex, new packaging techniques are being developed to better protect the chip and enable greater functionality.
By way of illustration, just one type of an advanced packaging technique is known as 3D packaging. This involves stacking multiple chips vertically, enabling greater processing power and reducing the amount of space required for the chip.
Another example is fan-out wafer-level packaging, which involves mounting the chip on a thin wafer and then spreading out the connections to the circuit board. This allows for more connections and greater functionality, without increasing the size of the chip.
The need for automation is increasing in the space as well. This technique can improve efficiency, reduce costs, and increase the accuracy of manufacturing processes.
For instance, let’s contemplate the use of robots in chip manufacturing. These automatons can handle delicate and precise tasks, such as the placement of components on the chip, without risking damage to the chip.
And then there’s the use of artificial intelligence to consider. It can be used to analyze data from manufacturing processes, identify patterns, and predict potential issues before they occur.