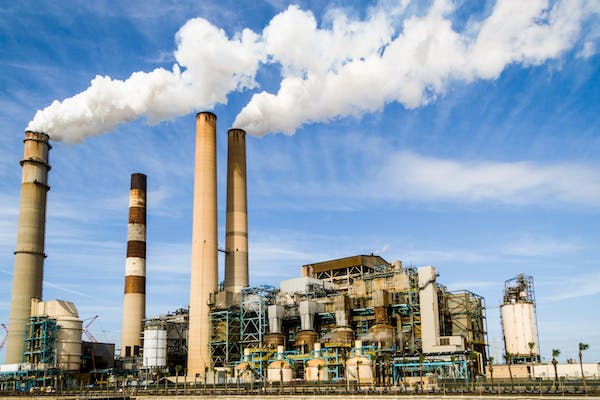
25 Jun MANUFACTURING FUTURIST: WHAT’S THE FUTURE OF THE FACTORY AND INDUSTRIAL CENTERS?
Reviewing manufacturing futurists’ and keynote speakers’ insights, it’s clear that the manufacturing sector is in the throes of mass transformation, driven by a wave of technological advancements and a changing global economic landscape. As we often remind speaking audiences ourselves, and touch on as manufacturing futurists, more than a few emerging trends and innovations are radically reshaping factory operations, creating a more efficient, adaptable, and sustainable industrial environment.
For instance, we’re well into the emergence of Industry 4.0, or the fourth Industrial Revolution, as it were. The means an increasing focus is occurring on the integration of the Internet of Things (IoT), cloud computing, artificial intelligence (AI), and machine learning into factory operations. By enabling real-time data collection, predictive analytics, and smart automation, Industry 4.0 technologies are paving the way for smart factories where production efficiency is maximized, and downtime is minimized.
Closely linked to the rise of Industry 4.0 is the surge in collaborative robotics or “cobots.” Such offerings are designed to work alongside humans in a shared workspace, performing repetitive or dangerous tasks and leaving more intricate and creative tasks to their human counterparts. As manufacturing futurists have noted, cobots are equipped with advanced sensors and AI algorithms that allow them to learn from their environment and improve their performance over time. Companies like Universal Robots and Boston Dynamics are at the forefront of this revolution.
Meanwhile, additive manufacturing, more commonly known as 3D printing, is no longer a fringe technology. It’s moving into the mainstream, with factories using it for everything from prototyping to producing end-use parts. In effect, 3D printing enables rapid production changes, reduces material waste, and allows for the creation of complex geometries that would be impossible with traditional manufacturing methods.
Digital twinning is another promising innovation in factory operations. The practice revolves around creating a virtual replica of the physical factory, enabling operators to simulate different scenarios, optimize operational efficiency, and predict issues before they occur. By mapping out the entire production process digitally, manufacturers can trial new ideas and troubleshoot problems without disturbing actual operations.
On the sustainability front, green manufacturing is also gaining significant momentum. Fueled by a combination of regulatory pressure and consumer demand for eco-friendly products, factories are adopting cleaner, energy-efficient technologies, waste reduction strategies, and circular production methods. Examples of this include solar-powered factories, zero-waste production lines, and factories that incorporate recycled materials into new products.
The concept of microfactories is also gaining traction. These small-scale facilities leverage automation and flexible manufacturing systems to produce a wide variety of products, often in closer proximity to end consumers. This approach reduces transportation costs and allows manufacturers to respond more quickly to market changes.
On other fronts, advances in augmented reality (AR) and virtual reality (VR) are providing innovative solutions for training and problem-solving. Using AR glasses, factory technicians can receive real-time information and instructions while working, dramatically reducing errors, and increasing safety.